Auto
ECO Green Bus eyes Nigerian market with full range
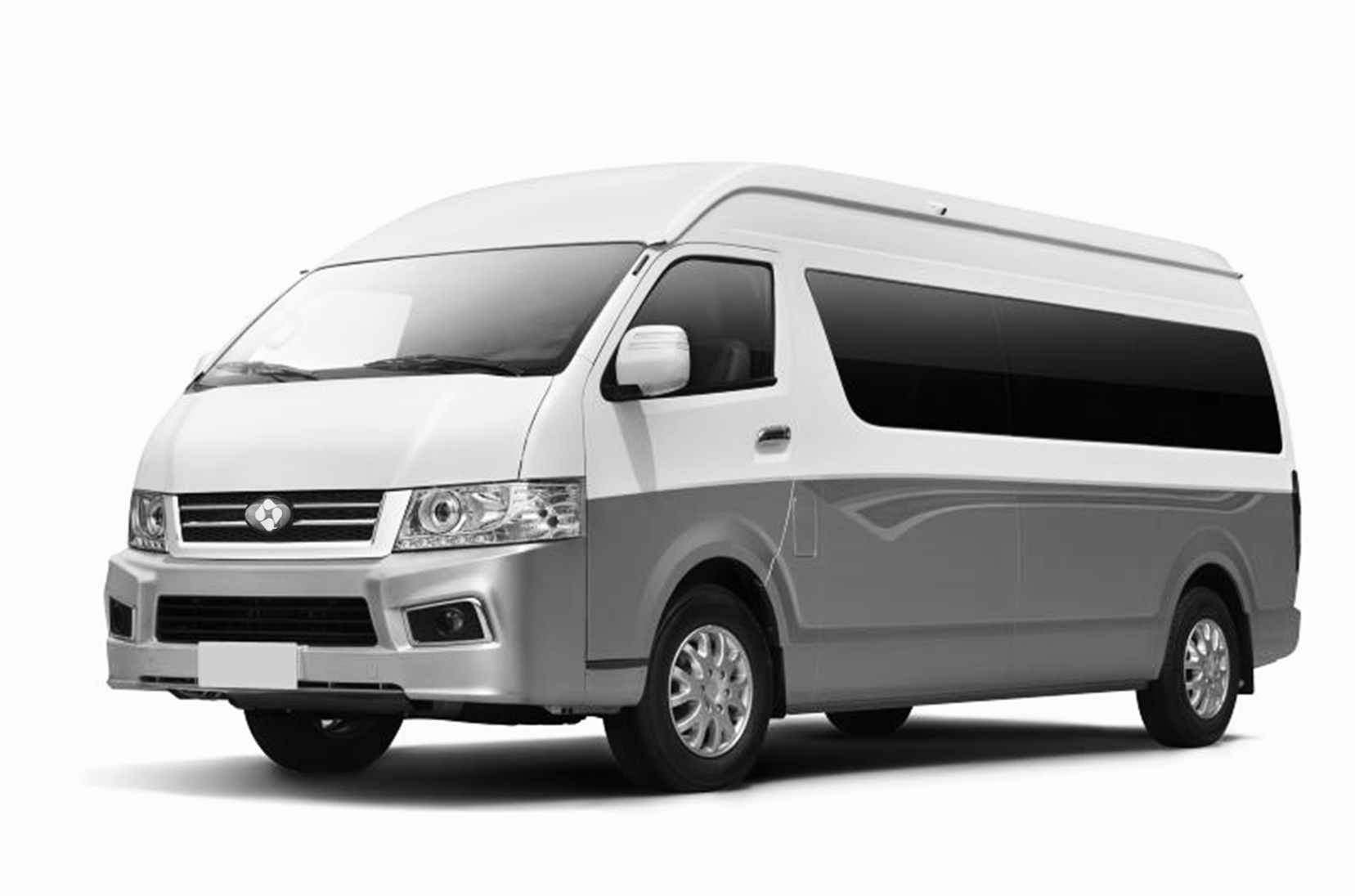
Natural gas-powered vehicle manufacturer, Austrian Technologies Nigeria, says its full models of ECO-Green buses are set to hit the Nigerian market.
It says the buses built with European standards for critical climate and infrastructure are targeted at private and public transport operators in Nigeria including schools and corporate organisations.
Chief Executive Officer of Austrian Technologies Nigeria Limited, Johann Rieger, who gave details of the full range says the buses are on a single platform comprising 8.5m length (Marcopolo size) for 60 passengers; 10.5m for 80 passengers, 12m for 100 people, 12.8m for 110 passengers and 18m accommodating 160 passengers.
The standard at ECO Green Buses is a monocoque chassis-body structure with advanced frame safety technology.
The core is a 3H high-strength body with front and rear buffer beams, roll-over safety frame and absorbed energy structure.
The key advantages of this technology are-higher safety for passengers through optimized distribution of impact forces through overall of body frame structure; improved life span of structure; lower operating costs (maintenance, tyres, fuel consumption); and the weight advantage over a classical chassis-body structure.
The whole-vehicle runs through an 18 stage E-coating process (cathode electrophoretic coating) for corrosion protection.
The electrophoretic paint becomes a layer of even, smooth, and strong adhesive paint film on the surface of body frame after electrochemical reaction. It makes the surface of body frame and inner cavity of being strongly anticorrosive, antirust, salt fog resistant and heat moist resistant and antirust of up to 12 years.
All buses come with maintenance free DANA axles and adjustable Front and rear air suspension with FIRESTONE air bags. All wheels have disc brakes with automatic slack adjuster from KNORR in combination with WABCO ABS. This high European safety standard improves safety and reliability of buses and supports operations by high availability of buses through reduced down time and shortened time of maintenance. The life span of these components is a multiple of the normally applied low-cost components.
A tyre pressure montoring system with display on instrument panel and full integration into the ECO Telematics system is standard and one of the core safety features of ECO Green Buses. BOSCH power steering is one of the world’s safest steering systems for commercial vehicles.
The cockpit is highly ergonomic. The combination of the fully integrated digital cockpit and employment of high-quality European core components are just some of the key factors that make ECO Green Buses efficient and safe.
The driver receives direct feedback in real-time on his/her behaviour in safety and economic driving through the digital dashboard and ECO Telematics system.
The possibility to convert gas buses to zero emission hydrogen operation upon local availability of hydrogen is another unique feature of ECO Green Buses. Bus structure, gas supply chain and safety equipment are already prepared for such conversion at little effort and costs.
The MD said the buses are the safest and most economic mass transit vehicles which could reduce carbon footprints by 95 per cent and operating cost by 30 per cent.
He said, “We also have 5.4m (Hiace type) as well as 6.5m and 7.5m (Toyota Coaster) type buses.” It is crucial for the further development of Nigerian transport sector to include and onboard Danfo operators and other stakeholders into the public transport operations.
Rieger noted that the buses are equipped with gas engines of higher emission standards (Euro 5) with no toxic, smog or smoke, guaranteeing reduced noise and lower fuel costs
Some of the unique features of an ECO-green bus are given as roof mounted CNG cylinder with up to 500km range and gas leakage detection system; tyre pressure monitoring system; two emergency roof hatches (front/rear); fire extinguisher in driver’s cabin, automatic fire extinguishers in engine compartment; all disc brakes with automatic slack adjuster and the ABS.
Others are speed limiter, alcohol test and driver’s fatigue detection with driver’s biometric identification, CCTV camera system that can be directly integrated into the city surveillance system; reverse camera; handicapped ramp and wheelchair area.
All buses are equipped with ECO Viroxx air purification system, a bipolar ionization system integrated into the ventilation system of ECO Green Buses. It is the only system worldwide that permanently and chemical free sanitizes the indoor air in buses throughout the entire operation.
The ECO Viroxx bipolar ionization technology is clinically proven to inactivate up to 99.999% of COVID-19 and other viruses and germs. SARS-Corona viruses can be rendered completely harmless at the molecular level by destroying the structure of their virus surface, envelopes, and tips.
High-energy ionization of the cabin and the production of a bipolar aerial ionization network can achieve a natural air disinfection rate of over 99.999 per cent (log 5). This process inactivates or eliminates viruses, germs, bacteria, molds and eliminates unpleasant smells.
Rieger said, “Up to 70 per cent of all components of the ECO-Green buses should be manufactured or assembled locally within five years of operation including the first green engine.”
Additionally, the company offers bus Simulator, bus scanners, telematics and ICT and intensive training of drivers and maintenance personnel to assure proper maintenance of vehicles.
Auto
Excitement as Chery celebrates innovations through roadshow at The Palms

Excitement as Chery celebrates innovations through roadshow at The Palms
Excitement is in the air for all new car fans as the much-anticipated Lagos Chery Road Show holds tomorrow (Friday) April 26, 2014.
Carloha, a renowned automobile dealer of Chery vehicles in Nigeria, announced this in a statement, saying it will be an unparalleled automotive all the way from the auto firm to The Palms, the venue of the main event.
It also the event would offer an unforgettable journey of celebrating innovation, style, and the thrill of the open road.
Part of the statement read, “The Chery Road Show promises to be an electrifying extravaganza, offering attendees a thrilling journey through the heart of Lagos, celebrating innovation, style, and the spirit of adventure.
“Kicking off from the Carloha Showroom in Alapere, Lagos, the procession will wind its way through Anthony Village, Maryland, and the vibrant Sheraton Hotel axis, before making its grand entrance into the bustling streets of Opebi-Allen, and divert to Ikoyi, Victoria Island.
“The convoy will culminate at the The Palms, where the main event will take place.”
Giving highlights of roadshow, it says, “The sip and paint session promises to be a delightful fusion of creativity and relaxation.
“Set against the dynamic backdrop of Carloha Parking Lot at the Palms, participants will unleash their inner artists while watching with keen expectation on the artiste while creating masterpieces that capture the essence of the Chery brand.”
The firm also promised to provide the latest offerings from Chery with interactive displays showcasing the brand’s cutting-edge technology, superior craftsmanship, and commitment to excellence.
The Chery impressive lineup of vehicles at the venue, it added, would show why the brand had continued to redefine the automotive landscape.
“Immerse yourself in the festive atmosphere as you mingle with fellow enthusiasts and soak in the excitement of this one-of-a-kind event.
“Take advantage of exclusive offers and promotions available only at the Chery Road Show.
“Whether you’re in the market for a new vehicle or simply seeking to elevate your driving experience, don’t miss this opportunity to explore unbeatable deals and incentives,” it stated.
The statement reminded that Carloha Nigeria offers six-year free service, and six-years warranty or 200,000 kilometres, whichever comes first.
It also stated that the admission to the Chery Road Show was made free to give a lot of people the rare opportunity to experience the ultimate automotive extravaganza.
Auto
African automakers, minister, NADDC DG for June 27 Nigeria industry summit
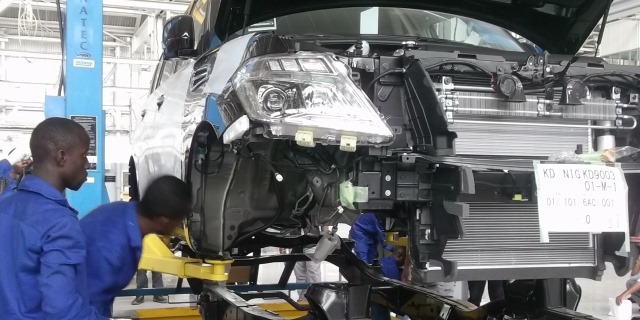
African automakers, minister, NADDC DG for June 27 Nigeria industry summit
A delegation of the African Association of Automotive Manufacturers (AAAM) from South Africa is expected in Nigeria on June 27 this year to attend the maiden edition of the Nigeria Auto Industry Summit (NAISU).
The team will be joined by the Nigeria Association of Automotive Manufacturers (NAMA) team and other leading stakeholders to brainstorm on the sector’s development in the country and by extension Africa.
The organisers of the event, Nigeria Auto Journalists Association (NAJA), disclosed this in a statement, adding that it would be organised in partnership with the National Automotive Design and Development Council (NADDC).
Scheduled to hold at Radisson Hotel, Ikeja, Lagos, on Thursday, June 27th, 2024, the summit is envisioned as an annual flagship event of the country’s automotive industry to rally all stakeholders together to explore the great potential in the automotive sector for national development.
It said the maiden edition of the event would be declared open by the Minister of Industries, Trade and investment, Dr Doris Uzoka-Anite, under the theme ‘Reviving Nigeria’s Economy through the Automotive Sector’ .
It would have the NADDC Director General, Mr. Joseph Osannipin, as the chief host, it stated.
Commenting on the importance of the summit for the development of the country’s automotive sector, Chairman, organizing committee of NAISU, Femi Owoeye, said, “Initiating this summit is vital, especially at this moment in history, when Nigeria is struggling to map its way out of the prevailing global economic despair.
“Being one of the drivers of the global economy, the automobile industry, if given the necessary impetus in Nigeria, is capable of transforming the country to an automotive manufacturing hub in Africa.
“To this end, Nigeria Auto Industry Summit shall annually produce significant information that would help the government to make it happen.”
On his part, Chairman of NAJA, Mike Ochonma, said, “Significantly, the summit shall bridge the information and communication gap between the nation’s auto industry stakeholders and relevant government agencies.
“Moreover, annually, the summit shall give a single and united voice for the auto industry leaders to set developmental agenda aimed at kick-starting and driving relevant government policies towards a sustainable development of the automotive industry in Nigeria and ultimately position the country as a frontline beneficiary of the African Free Trade Agreement Area.”
Auto
FG to roll out 200 CNG buses, 2,500 tricycles next month

FG to roll out 200 CNG buses, 2,500 tricycles next month
- Targets one million automobiles
The Federal Government says it will unveil its first set of Compressed Natural Gas (CNG) vehicles and tricycles for mass transit next month (May 2024), as part of activities to mark President Bola Tinubu’s one year in office.
Special Adviser to the President on Information and Strategy, Bayo Onanuga, in a statement on Sunday said 200 buses and 2,500 tricycles powered by CNG would be unveiled.
He said the buses and tricycles would be rolled out with a set target of one million CNG-powered automobiles by 2027.
He said the committee led by Michael Oluwagbemi was set to deliver cheaper, safer and more climate-friendly energy vehicles.
Onanuga said the committee had fulfilled some foundational reforms to enable the new CNG and electric vehicles to deliver the future Tinubu promised.
He added that all was ready for delivery of the first set of critical assets for deployment and launch of the vehicles ahead of the first anniversary of the Tinubu administration on May 29.
Onanuga also said, “In collaboration with the private sector, the PCNGI is set to deliver 100 conversion workshops and 60 refuelling sites spread across 18 states before the end of this year.”
The Federal Government provided N100 billion, as part of the N500 billion palliative budget, to purchase 5,500 CNG vehicles, being part of the many intervention programmes to cushion the effect of increase in petrol pump price on the masses.
This included buses and tricycles, 100 electric buses and over 20,000 CNG conversion kits, with the development of CNG refilling stations and electric charging stations.
Onanuga said with necessary tax and duty waivers approved by Tinubu in December 2023, the private sector partners in the Presidential CNG Initiative (PCNGI) had responded with over $50 million investments in refuelling stations and conversion centres
He stated, “Also, a safety policy document on 80 standards and regulations that must be strictly adhered to by operators has been developed and approved to ensure CNG conversions are done safely and reliably.
“The deployment of CNG buses and tricycles and the vision to get at least one million natural gas propelled vehicles on our roads by 2027 will mark a major energy transition in our country’s transportation industry.
Onanuga also said, “Four plants owned by JET, Mikano, Mojo, and Brilliant EV located in various parts of the country are involved in the assembly of the Semi Knocked Down (SKD) components of the CNG buses.
“JET, which has received the SKD parts, is coupling the buses in Lagos and is working towards delivering 200 units before the first anniversary of the Tinubu administration.
“Brilliant EV will assemble electric vehicles. It is awaiting the SKD parts, which will arrive in due course. The electric vehicles it will produce are meant for states, such as Kano and Borno, which do not have access to CNG for now.
“They will also be available in key Nigerian cities and university campuses.
“It must be noted that soon to be completed gas pipeline projects initiated by the Buhari administration and being completed by NNPCL (the AKK Pipeline) will take gas into the hinterlands of North-East and North-West where there is current paucity.”
He said over 600 buses were targeted for production in the first phase this year while a new plant on the Lagos-Ibadan Expressway would assemble thousands of tricycles.
“The SKD parts manufactured by the Chinese company LUOJIA in partnership with its local partner to support the consortium of local suppliers of CNG tricycles are set for shipment to Nigeria and expected to arrive early in May. About 2,500 of the tricycles will be ready before May 29, 2024.
“Thousands of conversion kits for petrol powered buses and taxis that want to migrate to CNG are also ready with CNG cylinders.
“The Federal government intends to provide them at subsidised rates, especially to commercial vehicle drivers to bring down the cost of public transportation.”
As part of private sector collaboration, NIPCO and BOVAS are involved in offering refilling services for the CNG vehicles and also serving as conversion centres.
NIPCO is setting up 32 stations nationwide to offer the services. The company has completed the set-up of four of the CNG stations.
“Likewise, BOVAS is setting up eight stations in Ibadan, two each in Ekiti, Abuja and four in Ilorin.
“MRS is also involved. It is making efforts to announce where its refilling stations and conversion centres will be,” Onanuga added.
He also said NNPC Limited, which had launched an on-and-off CNG initiative in the past, was joining the new initiative and expected to announce the locations for CNG refilling and CNG conversion centres nationwide.
The statement said PCNGI was working with 22 other agency-partners, including the Standards Organisation of Nigeria (SON) and National Automotive Design and Development Council, to deliver 80 Natural Gas Vehicle Conversion and Associated Appliances Standards for the country.
He added that the vision of the President to deliver one million gas vehicles could not be possible without the private sector, including the RTEAN, NURTW and players in the downstream sector of the transportation chain and financiers.
-
Education6 days ago
Why we charge N42m fees for primary school pupils — Charterhouse Lagos
-
Auto6 days ago
We expect massive roll-outs of Nigeria-made cars by December 2024 – Minister
-
metro6 days ago
JUST IN : Borrow pit collapses, kills seven Qur’anic school pupils
-
News6 days ago
We’re not part of Yoruba Nation agitation, says MKO Abiola family
-
metro4 days ago
How gunmen killed Babcock university lecturer, abducted two – Police
-
Politics6 days ago
Ondo APC primary: Ododo, gov aspirant in open confrontation
-
Business7 days ago
N50,000 presidential grant: 100,000 small businesses benefit in first phase
-
Sports6 days ago
Arsenal beat Wolves to return to top spot